top of page
MAGNETIC SECURING SYSTEM
Aligner System Sub-Project
Within the Aligner System build project, I was also tasked with redesigning the securing system for the packages. The first iteration of the aligner system relied on the use of vacuum to prevent fibers from moving during the alignment and epoxy process. Although due to discrepancies in material finishes, the hold-down force began to deteriorate. My objective was to redesign the securing method on the system while allowing for seamless integration with existing hardware and custom components. I decided to use a pneumatically driven magnetic gripper. This would ensure that in the unfortunate event of power or air being cut from the system, the fibers stay secured.
Magnetic Securing System: Text
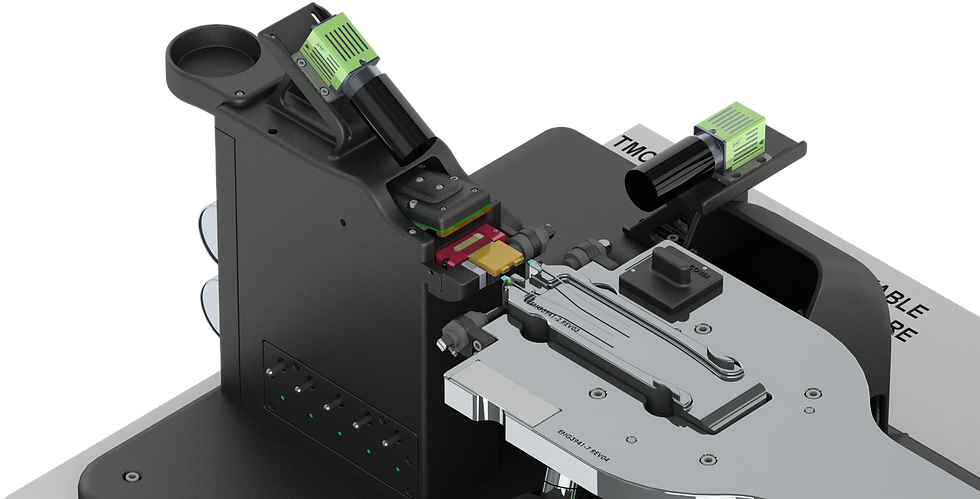
Magnetic Securing System: Image
Component Diagram:
Magnetic Securing System: Text

Magnetic Securing System: Image
The smooth integration onto the existing system was made possible by constraining my design to the unused space at the center of the hexapod positioning system. I then designed a mechanically adjustable stage that helped to secure the magnetic gripper to the hexapod plate. This allowed for variability in the hold-down force and ensured the magnetic gripper face maintains parallelity with the magnet retainer. Of which I redesigned to provide maximum interactive surface area and reduced overall weight.
​
Contributions:
Ground-up redesign of nest securing mechanism.
Seamless integration onto existing infrastructure.
System ready for production deployment.
​
Magnetic Securing System: Text
bottom of page