UNDERWATER ROV TEAM
Remotely Operated Vehicles Team
At the start of my sophomore year, I decided to join the Underwater Remotely Operated Vehicles Team at Linn Benton Community College. Their mission was to design an ROV that was capable of competing in the Mate International ROV competition. The Marine Advanced Technology Education (MATE) Center set forth various tasks that each ROV must be able to complete in a given time period. The tasks were based on real-world issues and applications that ROV's encounter, although modeled through mock props made of PVC pipes and other various components. These tasks involved identifying an aircraft based on the pattern on the tail wing. Removing debris from an aircraft engine and recovering the aircraft's engine from the pool floor. Installing a seismometer and processing the data from the device on the surface and installing a tidal turbine. As well as various other side tasks along the way.
​
My first task on the team was to help design a new frame for the ROV. We decided to construct the frame out of 80/20 T-Slotted extrusion aluminum. Allowing us to have a very dynamic system, which could easily add attachments and adjust the size of our ROV to accommodate various components as they developed over the lifespan of the project.
​
The next project I was tasked with involved designing a Printed Circuit Board (PCB) that would allow us to convert our 48VDC-10A power supply to 12VDC-33A. I designed the board using the program KiCad. After completing the board design I sent the file over to a local PCB manufacture, OSH Park. The completed board design can be seen below.
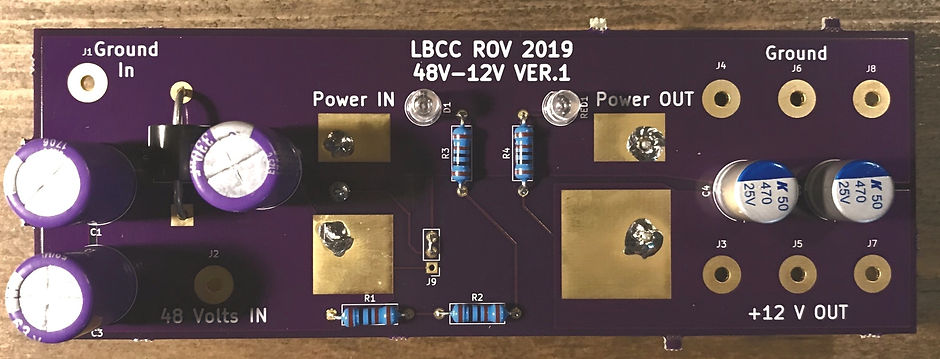
ROV Sub-Systems
After a few months of working with the team, I became the mechanical sub-team lead. Meaning I oversaw all the mechanical projects related to the ROV. While working as a team lead I also designed various sub-systems including:
Winch System: Used in recovering Mini-ROV for pipe inspection.
Propeller Covers: Ensured Mini-ROV propeller integrity.
Trout Release System: Allowed for the remote release of simulated trout at a specific location.
Camera Housings: Enclosed system allowing cameras to be epoxied with clear semisphere lenses.
Final ROV Design
The final design of our ROV can be seen in the schematic below. Although there are a few systems not shown in the model for simplicity. Sub-systems not included in the schematic include:
​​
Variable buoyancy system.
Fixed buoyancy system.
Trout Release System.
Mini-ROV.
Main tether.
​
You will notice in the images from the competition the use of multiple water bottles being used as buoyancy devices, this was due to a system failure in our original fixed buoyancy, requiring us to adapt and overcome using available resources. (ie: Water bottles that were given to us as gifts from MATE during the competition.)

MATE 2019 International Competition
In the Spring of 2019, our team qualified for the MATE International competition. Out of the 741 teams who participated in the competition, only 70 advanced to the international competition. Upon arriving in Kingsport Tennessee our team reassembled the ROV and completed safety checks. We participated in two product demonstrations over the weekend and ended up finishing in 18th place.
​
Contributions:
Designed and manufactured an improved chassis.
Functioned as the mechanical team lead overseeing 10 other students.
Designed and manufactured a Printed Circuit Board (PCB) to convert 48VDC-10A power supply to 12VDC-33A.
Designed and integrated various sub-systems on the ROV.
COMPETITION HIGHLIGHTS
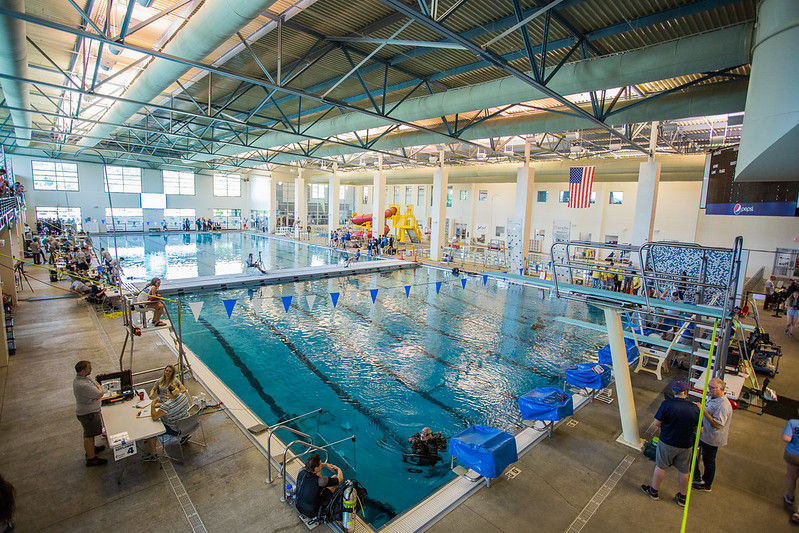


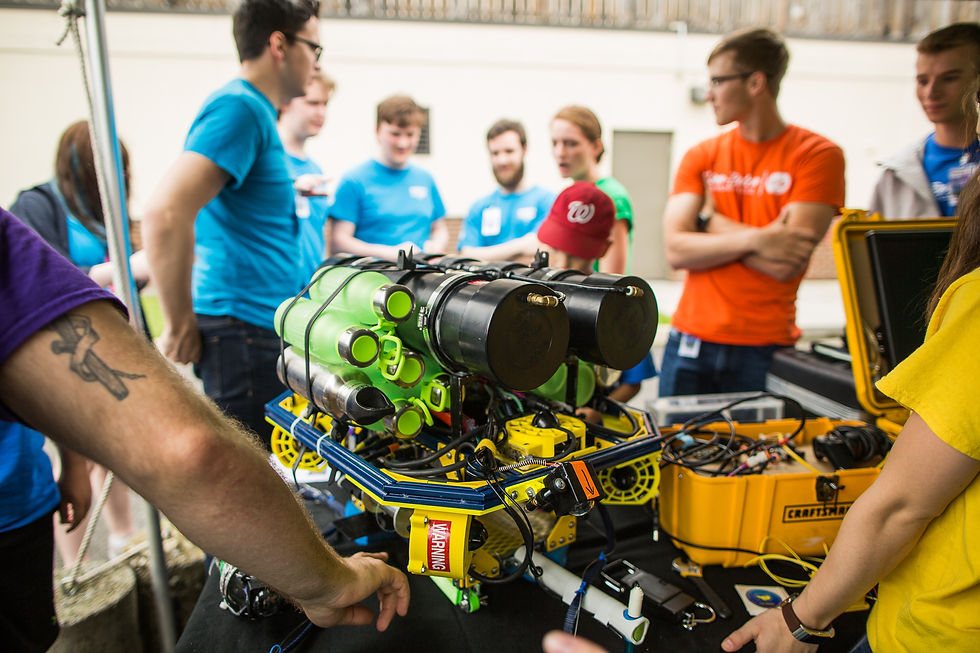
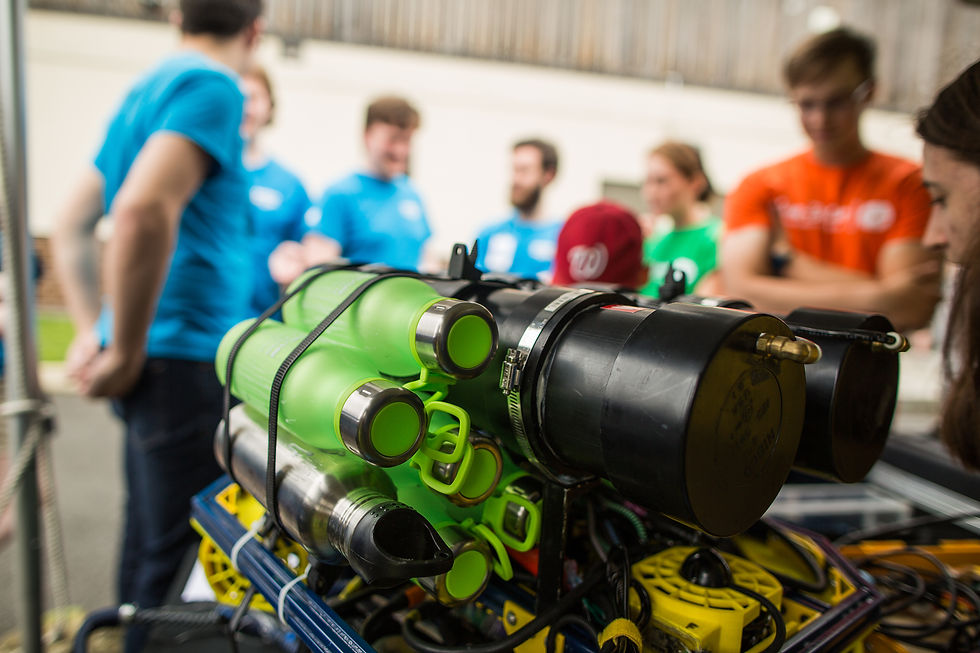

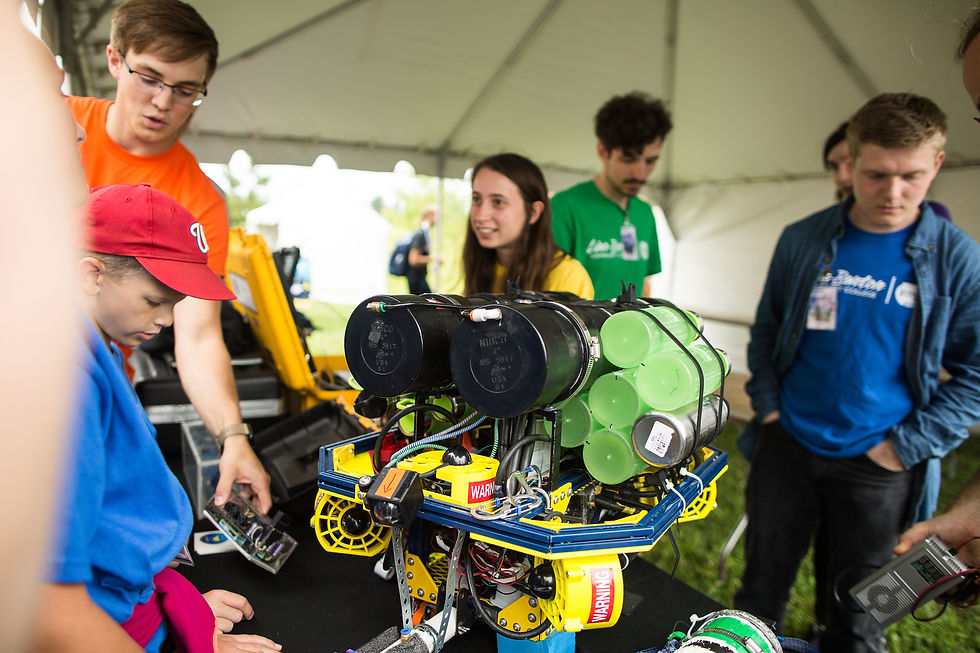

